WORKING PRINCIPLE
A Plug Flow Reactor (PFR), also known as a tubular reactor, is a type of continuous reactor where the reaction mixture flows like a "plug" through a tube. The key characteristic is that there is no axial mixing (along the length of the reactor) but perfect radial mixing (across the cross-section).
Reactants Enter the Reactor: The feed flows continuously into the reactor at a fixed rate.
Plug-Like Flow: The fluid moves in discrete "plugs" that do not mix with each other;Each plug reacts independently as it moves through the reactor.
Reaction Progression: As the plug moves forward, reactants are converted into products. The reaction rate varies along the reactor length due to changing concentrations.
Products Exit the Reactor: The fully reacted mixture exits the reactor at the other end.
.png)
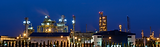
MAIN DESIGN FEATURES
SUNKAIER plug flow polymerization reactor process is an efficient, continuous method for producing polystyrene and related polymers. Its design ensures high conversion and consistent product quality, making it a preferred choice in industrial polymer manufacturing.
.png)
ABS, HIPS APPLICATIONS
SUNKAIER plug flow polymerization reactor process is a specialized method used in the production of polymers, particularly polystyrene and its copolymers (such as high-impact polystyrene, HIPS). This process is a continuous tubular (plug flow) reactor system for efficient polymerization.
Reactor Type:
Uses a plug flow reactor (PFR), which ensures minimal back-mixing and allows for a controlled progression of reaction stages.
The reaction occurs in a long, tubular system where monomers flow continuously while undergoing polymerization.
The reactor is maintained at elevated temperatures (~100–200°C) to initiate and sustain polymerization.
Pressure is controlled to keep the monomers in the liquid phase (if bulk polymerization is used).
As the reaction progresses, viscosity increases, requiring careful heat transfer to avoid hot spots.
Some versions may use multiple reaction zones with varying temperatures.
INDUSTRY
Polystyrene (PS) production.
High-impact polystyrene (HIPS) when rubber modifiers are added.
Copolymerization with other monomers (e.g., acrylonitrile, butadiene).

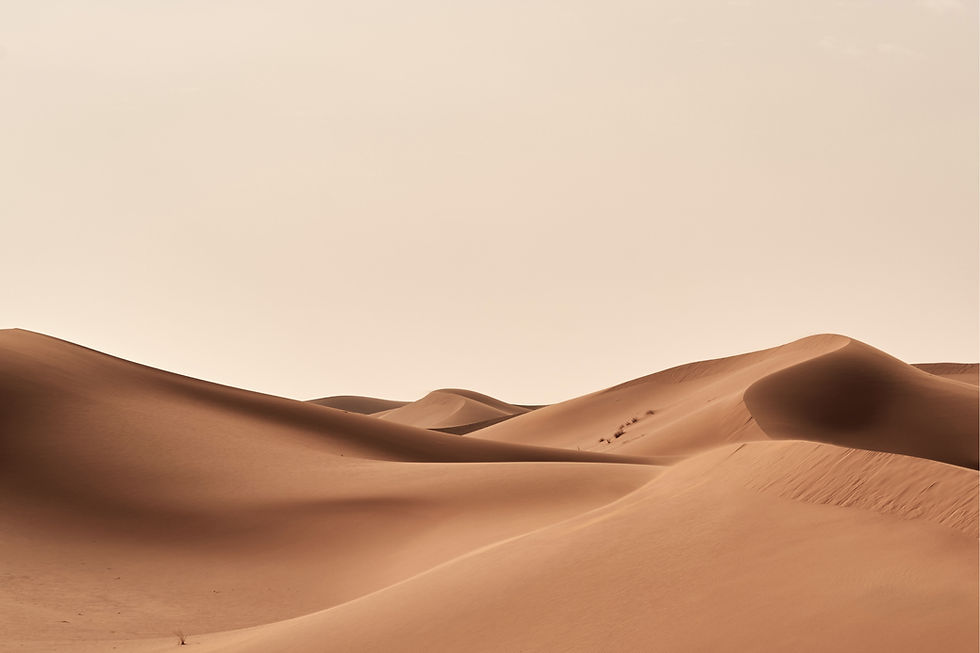
MODELS AND TECHNICAL SPECIFICATIONS
Model | Impeller Diameter (mm) | Motor Power (KW) | Rotational Speed (RPM) |
PFR1300 | 1300 | 55 | ~10 |
PFR1600 | 1600 | 90 | ~10 |
APPLICATION FIELDS
DOWNLOADS
DOWNLOADS
ENGLISH
ENGLISH
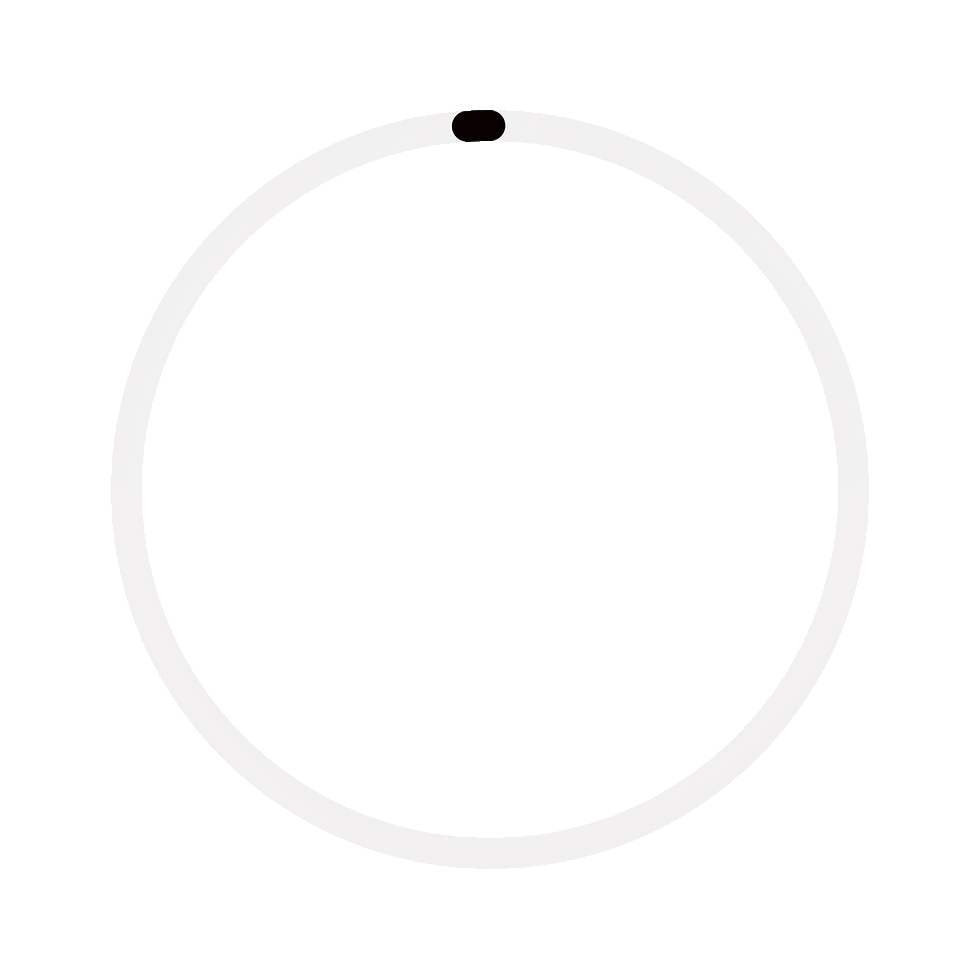
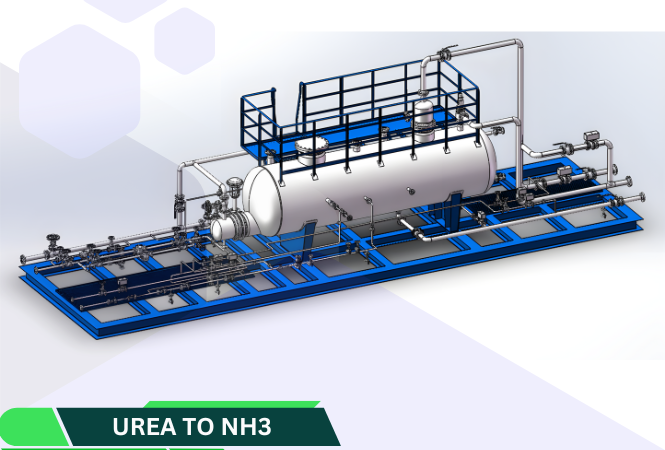
UREA TO AMMOUNIA
Collapsible text is perfect for longer content like paragraphs and descriptions. It's a great way to give people more information while keeping your layout clean. Link your text to anything, including an external website or a different page. You can set your text box to expand and collapse when people click, so they can read more or less info.
.png)
WFF EVAPORATOR
Collapsible text is perfect for longer content like paragraphs and descriptions. It's a great way to give people more information while keeping your layout clean. Link your text to anything, including an external website or a different page. You can set your text box to expand and collapse when people click, so they can read more or less info.
.png)
LAB REACTOR
Collapsible text is perfect for longer content like paragraphs and descriptions. It's a great way to give people more information while keeping your layout clean. Link your text to anything, including an external website or a different page. You can set your text box to expand and collapse when people click, so they can read more or less info.